Modern methods of construction
Magna Housing outlines the case for off-site modular building techniques versus traditional construction
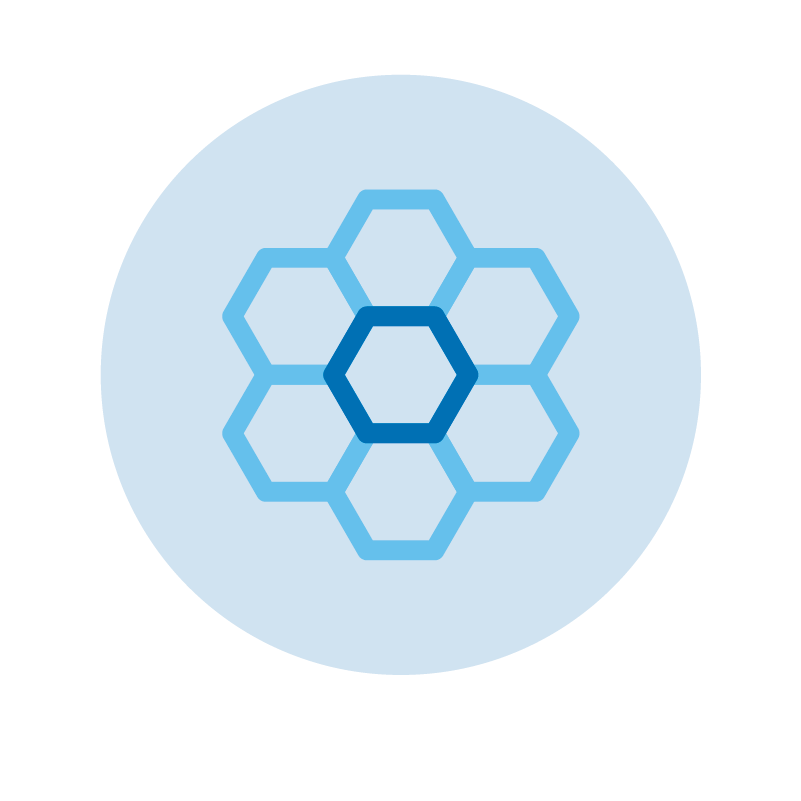
GROWTH, DEVELOPMENT & REGENERATION
Image: Magna Housing
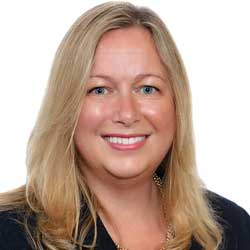
Selina White
CEO, Magna Housing
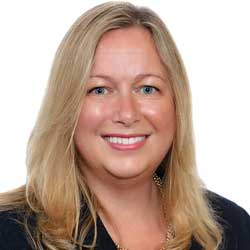
Selina White
CEO, Magna Housing
Issue 70 | February 2024
To read the industry media and follow the recent parliamentary inquiry (titled ‘What’s gone wrong?’), you would think it’s all doom and gloom for modern methods of construction (MMC). But there is a brighter story to tell, as our MMC journey at Magna shows.
Recently, I was sitting with two of our customers in their new MMC house, listening to them wax lyrical about their lovely, warm home. Meanwhile, one of their children had just bought a traditional new-build on ‘one of those big estates on the edge of town’ and was having all sorts of problems with quality and aftercare.
The performance gap
This goes to the essence of Magna’s drive to consider MMC as a route to creating homes when we returned to development in 2017. We spent a year looking at the business case for MMC and questioned:
- Could we get homes of consistent quality and eradicate traditional construction’s performance gap between design and build, which we were paying to rectify?
- Could we be planning-friendly and deliver a mix of homes that matched the beauty of our region’s towns and villages?
- And would we be able to work at scale by ensuring our narrow country roads in the South West of England would not be a barrier to delivering modular homes to sites?
Proving the concept
Visiting our customers’ homes and hearing their stories leaves me in no doubt that our approach is the right one.
To deliver the proof-of-concept phase of our MMC journey, we partnered with Dorset-based off-site manufacturer Rollalong. At its purpose-built factory, it manufactures buildings for the defence, education and healthcare sectors and now, residential housing, which are delivered and installed on site.
In 2024, MMC is business as usual for Magna. At the start of January, lorries carrying our next generation modules left Rollalong’s factory near Ringwood and wound their way through Dorset to the Isle of Portland. They climbed its steep hills and navigated its narrow roads to the site of the former Royal Manor Arts College, where they will form 41 new, affordable homes. These all-electric, ‘net zero ready’ homes are NHBC Accepts accredited, specified with the Future Homes Standard in mind, and designed against the Building for a Healthy Life design code.
Cost of MMC vs traditional build
With the well-publicised quality issues associated with the traditional homes model, it’s fair to say that as a sector we don’t yet know the true and final cost of a building approach fraught with such variable quality control. In 2019 we were comfortable to assert that the capital cost of MMC was around 20% more expensive than traditional methods, based on a small factory order. Today we are delivering to the higher net zero ready standards and that gap is disappearing or gone.
The factory environment poses fewer technical challenges to reach net zero-carbon than traditional build, with its deepening supply chain and quality control challenges. Bulk ordering, repetition, collaboration, aggregation, hedging against inflation and holding a stock of popular homes mean MMC becomes the cheaper option and, for us, is the route of least regret.
Building skills
This year, Magna and our partners are working with Weymouth College to bring together experience from clients, architects, employers’ agents, legal, asset management, procurement and manufacturing to design and deliver a fully funded, two-day MMC course, which will help to build the skills and capabilities to deliver and maintain MMC homes in our region.
For Magna, building homes using MMC is now relatively simple and straightforward, but we have invested several years on the proof-of-concept and business case to get us to this point. We are now committed to sharing our learning so other housing associations can benefit from our experience.
To follow our MMC story, search #MagnaBuilds on LinkedIn.
“For Magna, building homes using MMC is now relatively simple and straightforward.”